Implementation of 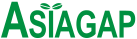
Model Cases
Next, we will look at the improvements seen at farms that have obtained certification by implementing ASIAGAP.
These are examples of the GAP initiatives implemented by the winners in the GAP category of the “Sustainable Agriculture for the Future Promotion Competition” taken from the Ministry of Agriculture, Forestry and Fisheries website.
Houmi Noko LLC
Farm management and management expansion using GAP since its founding
Basic Information
Location: Joetsu, Niigata Prefecture
Established: December 2005
Capital: 35.99 million yen
Staff: Two officers, 19 employees
Business Overview
Operating Area: 170 hectares (approx. 1,040 lots)
Main Crops: Paddy rice (ten varieties), etc.
Sales Destinations: Own sales company, JA Echigo Joetsu
Total Sales: Approx. 160 million yen(2020)
Certified Products: Rice (unhulled and unpolished rice)
Management Improvements
The following effects were achieved by using IT to perform the cultivation plan formulation, work records and results assessments required by GAP.
- Efficient usage of machinery was realized by spreading crop seasons especially for production of rice for the food service industry (rice transplanter 3.7 times, combine harvester 2.5 times operation) *1
- The cost of agorochemicals was reduced by placing orders with major agorochemicals suppliers for the necessary amount(2014 > 2016: 40% reduction) *2
- Seed and seedling costs were reduced (2014 > 2016: 14% reduction) by cutting reserve seedlings (amount of rice seeds) through efficient rice planting work based on cultivation plans *2
- personnel expenses were reduced(2014 > 2016: 35% reduction) through streamlined work based on detailed cultivation plans *2
- Work improvements originating with employees were implemented to improve employee autonomy.
As a result of these management improvements, in FY2016 rice production costs were 108,000 yen / 10a (down 5.4% from FY2014). Also note that certification costs were around 136 yen / 10a.
*1 Percentage of land area worked annually under the Niigata Prefecture Specified High Performance Agricultural Machinery Introduction Plan
*2 Comparison of expenses per 10a
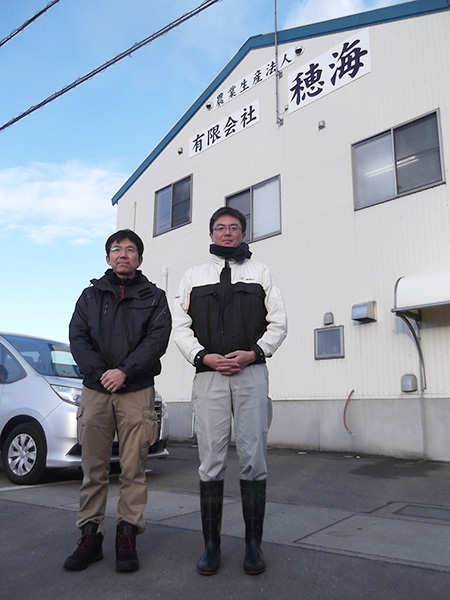
Marusei Orchard LLC
Obtaining GAP certification was utilized for employee training!
Orchard management that achieved recovery from the Great East Japan Earthquake
Basic Information
Location: Fukushima, Fukushima Prefecture Established: 2001 Staff: Three officers, four employees Part-time Staff: 11
Business Overview
Operating Area: Approx. 8 hectares
Main Produce: Cherries, peaches, apples, persimmons, grapes, pears, Japanese pears
Sales Destinations: tourist farms (direct selling, cafes), retail (AEON retail, etc.)
Total Sales: Approx. 90 million yen (2016)
Certifications Acquired: ASIAGAP Version 2 (fruit and vegetables), GLOBALG.A.P. (fruit and vegetables)
* Certified items are the same as the main produce (of which the underlined items are certified for GLOBALG.A.P. as well)
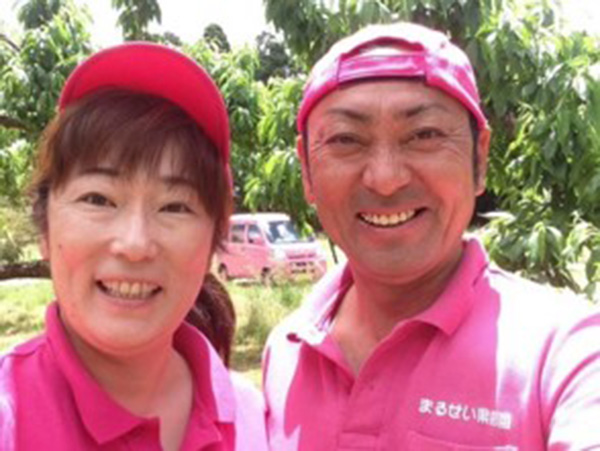
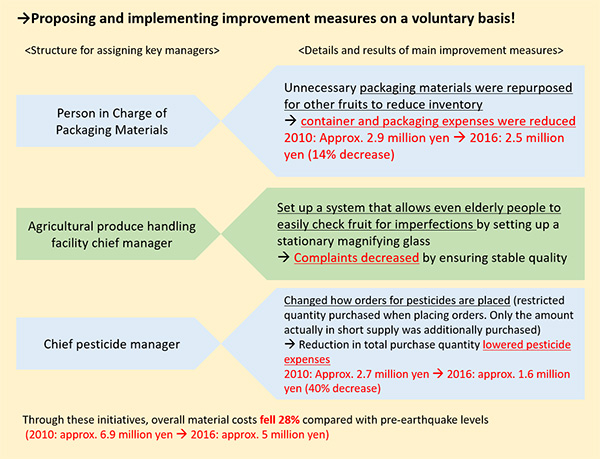
Saito Farm LLC
Working on GAP to achieve stable year-round cultivation!
Basic Information
Location: Tomisato, Chiba Prefecture
Representative: Tomohide Saito
Staff: 10 employees
Business Overview
Operating Area: 4.4 hectares (2.2 hectares of which are GAP-certified)
Main Crops: Komatsuna (Japanese mustard spinach), Chinese cabbage
Sales Destinations: Ito-Yokado, Ajinomingei, etc.
Total Sales: Approx. 65 million yen
Certified Products: Komatsuna
Management Improvements
The following effects were realized by formulating cultivation plans, recording work and streamlining work as required by GAP.
- Through the systematic formulation of cultivation plans, work streamlining and introduction of precoolers, the scale of operations was expanded and yields were increased (Operating Area 160a → 440a, Yield 100kg/day → 1ton/day)
- When accepting foreign technical interns, instructions were created in the native languages of the interns, meetings were held every morning, and efforts were made to improve the working environment and prevent accidents
- The results of soil diagnostics were utilized to reduce fertilizer expenses by 25%
By reducing the number of times agorochemicals were dispersed, pesticide costs were reduced by 60%
Revisions made to packaging materials and similar areas lowered packaging material expenses by 30%
(2013 to 2017) - Trade is conducted based on uniform standards for Saito Farm, and an efficient and stable harvesting and shipping system was established with the introduction of pre-coolers.
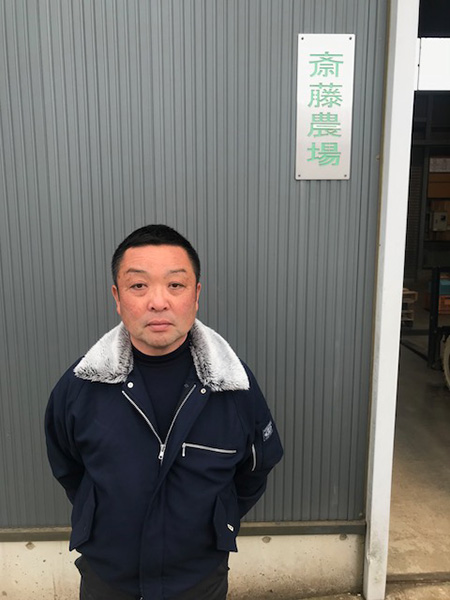
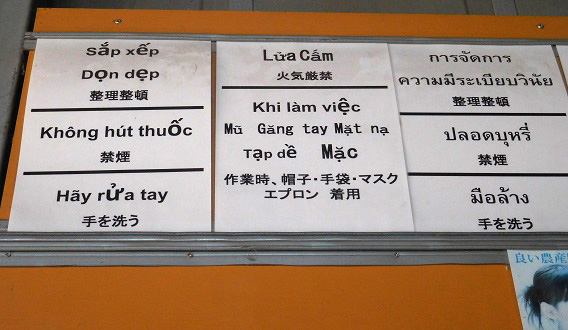
Greenhouse LLC
Utilizing GAP to become a top runner in the agricultural industry!
Basic Information
Location: Sanyo-onoda, Yamaguchi Prefecture
Representative: Masakatsu Matsumura
Staff: 44 employees, Special Skill 1 person (Thai),Foreign Trainee 3 persons (Thai)
https://zan-mai.jp/
Business Overview
Operating area: facilities - 4.9 hectares, open fields - 5.1 hectares
Main Crops: Green onions, bok choy, spinach, mini tomatoes, etc.
Business Partners: Markets in Yamaguchi Prefecture
Certified Products: Green onions, bok choy, spinach, mini tomatoes
Management Improvements
With the introduction of GAP, work became more efficient and was documented in manuals, resulting in higher productivity and increased motivation for young workers.
- Due to inventory control for production materials and the thorough revision of work processes, green onion turnover rate rose (from 3 to 4), making it possible to introduce other items and helping to stabilize management.
- By segmenting work and developing manuals, the work was streamlined, and the introduction of two full days off per week and other improvements lowered the personnel turnover rate among new employees.
- Due to the adoption of GAP, production costs as a percentage of production volume fell 37% (2014 to 2018) while production volume itself rose 44% (2014 to 2018).
- Once-weekly patrol meetings, monthly meetings and several training sessions each year were held fostering an awareness among all employees to work towards management improvements.
- A new packaging center incorporating GAP-based risk assessments was established (2018).
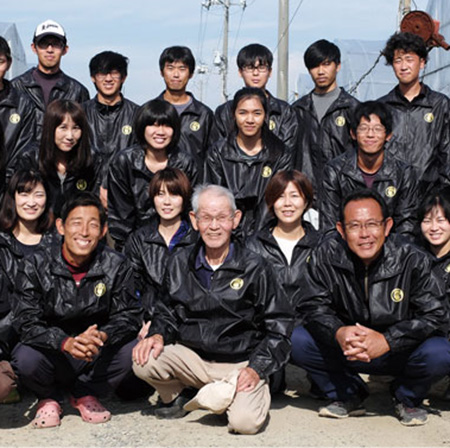
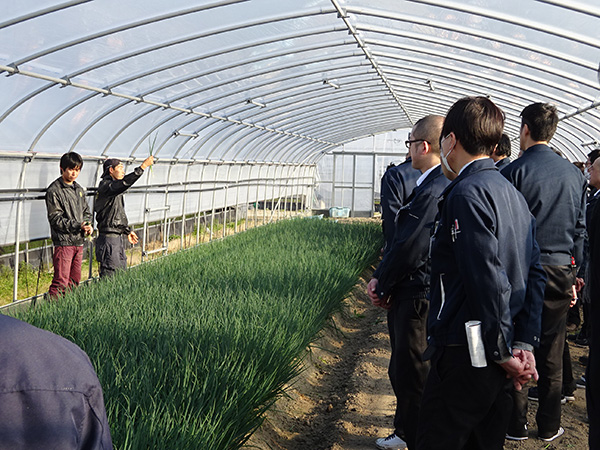
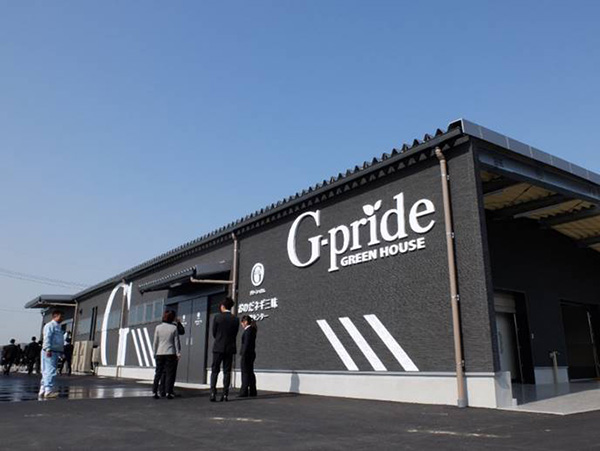